Our Team: Deep Manufacturing and Software Development Expertise
Nipun Girotra
President & CEO
Nipun Girotra is currently CEO, and Member of the Board of Directors of 1factory. Prior to founding 1factory, Nipun held multiple roles in manufacturing and operations management at Novellus Systems and Applied Materials.
Nipun holds a Bachelors degree in Mechanical Engineering from the University of Pune, a Masters degree in Industrial Engineering from Georgia Tech, and an MBA from The Wharton School at the University of Pennsylvania.
Oleg Nickolayev
Chief Technology Officer
Oleg Nickolayev is currently Chief Technology Officer, and Member of the Board of Directors of 1factory. Oleg has deep experience in all tiers of web application development, complex data integration, and big data analytics.
Prior to joining 1factory, Oleg worked for Oracle Corporation, Rearden, and Elementum SCM. Oleg holds an MS in Engineering from Dartmouth, and an MS in Computer Science from University of Illinois at Urbana-Champaign.
Dr. William Stallard
Vice President of Engineering
Dr William Stallard is currently Vice President of Engineering at 1factory. Will has over 20 years experience building enterprise software at Oracle Corporation (CASE Tools, ERP applications, integration middleware, and workflow management solutions), and goBalto (acquired by Oracle)
Will holds a BSc in Physics from Imperial College, London and a Ph.D. in Semiconductor Physics from the University of Exeter.
Michael Corrales
Vice President Sales & Marketing
Michael Corrales currently holds dual responsibilities for Sales Operations and Marketing at 1factory. Michael brings over 15 years of experience in manufacturing, business development, supply chain management, and business analytics.
Prior to joining 1factory, Michael held multiple operations roles at Schunk-Xycarb, and Cortec Precision. Michael holds a Bachelors Degree in Liberal Arts from San Jose State University.
Nick Kelly
Vice President of Product Management
Nick Kelly is currently Director of Product Management at 1factory. Nick brings deep quality engineering and management experience to his role as Product Manager.
Prior to joining 1factory, Nick held quality engineering and management roles at PNA Molding and Magnet-Schultz of America. Nick holds a Bachelors Degree in Applied Engineering and Technology from Eastern Illinois University
Matt Stanley
Director, Customer Success & Partnerships
Matthew Stanley is currently Director of Customer Success and Global Head of Partnerships at 1factory. Matthew brings over 17 years of experience with quality control and quality systems administration in automotive and aerospace manufacturing.
Prior to joining 1factory, Matthew held multiple positions at Acutec Precision Aerospace, Inc. including Quality Engineer, Quality Manager, Quality Planning Team Lead & Quality Improvement Project Manager.
Faith Thompson
Director, Operations
Faith Thompson is currently Director of Business Operations at 1factory. Faith has over 20 years of business operations, employee operations, and accounting experience. At 1factory, she manages all finance operations and leads the trade show and event marketing programs.
Faith has been a volunteer with the American Legion Auxiliary - non-profit supporting our veterans - for over 30 years. She is currently the President of a local unit, and is also the Treasurer for the Santa Clara District.
Ian Warren
Principal Engineer
Ian Warren is currently a Principal Engineer at 1factory. Ian has 15 years of experience with all aspects of developing complex software in the education, e-commerce, and the sports science problem domains.
Prior to joining 1factory, Ian worked at Nike building applications to support the R&D teams. Prior to Nike, Ian worked for the Northwest Evaluation Association. Ian holds a BSc in Mechanical Engineering from Oregon State University.
Long Ton That
Principal Engineer
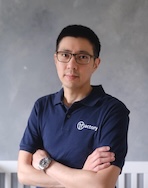
Long Ton That is currently a Principal Engineer at 1factory. Long has over 15 years of experience in full stack development, delivering robust and performant solutions tailored to meet customer needs.
Long's career began in customer support engineering — an experience that continues to inform his user-focused approach to development. Prior to joining 1factory, Long held software development roles at Nike and Jive Software. Long holds a Bachelors degree in Computer Science from Oregon State University.
Thach Abraham Nguyen
Software QA
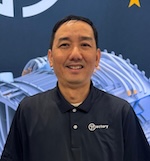
Thach Nguyen is currently a software QA engineer at 1factory. Thach has over 25 years of experience across manufacturing, quality (CMM programming), data warehousing and business intelligence.
Priori to joining 1factory, Thach worked for PNA Molding and Magnet-Schultz America in quality control roles where he used 1factory in his role every day. Thach holds a Bachelors Degree in Business Computing from Lotus College, Saigon and is studying towards a degree in Manufacturing Engineering.
Fabrizio Bertocci
Distinguished Engineer
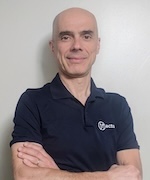
Fabrizio Bertocci is currently a Distinguished Engineer at 1Factory. Fabrizio has over 20 years of experience in research projects on high performance networking and developing commercial software.
Prior to joining 1Factory Fabrizio worked at Real-Time Innovations as a research principal engineer where he worked on several SBIR-related programs. Fabrizio holds a MS degree in computer engineering from University of Pisa (Italy).
Autumn Repetto
Director of QMS Products
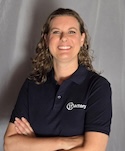
Autumn Repetto is currently Director of QMS Products at 1factory. Autmn has over 15 years of experience in Quality Management - including Auditing, Document/Record Control, CAPA Management, and FDA/ISO compliance.
Prior to 1Factory, she served as a Quality Manager at a novel Medical Device start-up, where she successfully guided the company to ISO 13485:2016 certification. Autumn holds a Bachelor's of Arts from California State University, Northridge.
Alexander Dementsov
Principal Engineer
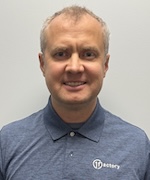
Alexander Dementsov is currently Principal Engineer at 1factory. Alexander has over 15 years of experience in full-stack software engineering.
Prior to joining 1factory, Alexander worked on a wide range of projects - a search index of 3D models for Physna, machine learning solutions for water utilities at Fracta, and tools for network services at Google. Alexander holds a PhD in Computer Science from Clarkson University.
Resellers & Global Technical Support
Pia Byrial
Byrial Holdings ApS, Denmark
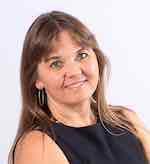
Pia Byrial is Founder and Owner of Byrial Holding ApS in Denmark. Pia has experience in building and implementation of Management Systems and Automotive Tools.
Prior to founding Byrial Holdings, Pia held roles at Hydro Aluminium, Eltwin Group, Bucher Municipal as Quality Manager/Director and also worked with implementation of 1factory in several companies before she became a 1factory consultant.
Pia has educations as Quality and Metrology Technologist and Quality Engineer.
Anand Bopardikar
EterQ Pvt. Ltd., India
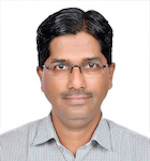
Anand Bopardikar is Founder and Owner of EterQ Solutions Pvt. Ltd. in Pune, India. Anand has deep manufacturing, QMS (ISO/IATF), quality control, maintenance, and new product introduction experience.
Prior to founding EterQ, Anand worked for Ashwini Magnets, Vanaz Engineers, Dugar Industries and Solutec.
Anand has many years of experience implementing and using 1factory as a customer prior to founding EterQ Solutions. Anand has a Bachelors Degree in Electrical Engineering from University of Pune.
Jochen Layer
KeyToData GmbH (K2D), Germany
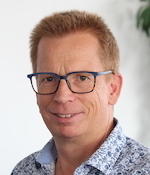
Jochen Layer is Managing Director and Owner of KeyToData GmbH in Germany. Jochen has a deep experience in engineering, manufacturing and quality software for manufacturing industries.
In his career, he has worked as a management consultant for international companies. Today, as Managing Director of K2D-KeyToData, he serves quality management software customers throughout Europe.
Jochen holds a Master degree in Mechanical Engineering from the University of Stuttgart, Germany.
Luca Cariglia
ES-Tek srl, Italy
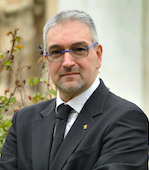
Luca Cariglia is co-founder and co-owner of ES-Tek srl in Villaverla (VI), Italy.
ES-Tek is a company specialized in develop, sales and support of software solutions for the design and quality control in the mechanical field.
Luca has been delivering CAD/CAM solutions and software development for nearly 30 years (prior experience includes Cadkey Inc, Kubotek Corp.). In last years, with his team in ES-Tek, he expanded his working area adding quality control solutions and consultancies.
Advisors
Kevin Jennings
Manufacturing & Supply Chain
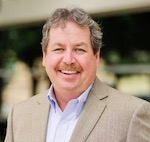
Mr. Jennings most recently served as Senior Vice President of Global Operations at Lam Research (Semiconductor capital-equipment manufacturer with $17B Annual Revenue) where he was responsible for worldwide manufacturing, supply chain, logistics, and facilities.
Prior to Lam Research, Mr.Jennings held a variety of executive roles covering engineering, business development, marketing, product line general management, and operations at Novellus Systems, preceded by management roles at KLA and Applied Materials. He earned an M.B.A. from Pepperdine University and an undergraduate degree in Electrical Engineering Technology from DeVry University.
John Flaig, Ph.D.
Statistics & Analytics
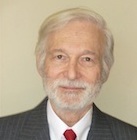
John J. Flaig, Ph.D. is a Fellow of the American Society for Quality (ASQ). His industry experience spans more than forty years, and includes roles at Apple, Applied Materials, and Hewlett-Packard.
Dr. Flaig was formerly a member of the Editorial Board of Quality Engineering, a journal of the ASQ. He holds a doctorate in engineering from California Southern University, a master's degree in mathematics from the University of California, and a bachelor's degree majoring in mathematics and economics from California State Polytechnic University. Dr. Flaig received the 2012 Distinguished Alumnus Award from Cal Poly's College of Science.
The 1factory Story
The Origin
1factory was founded based on the deep manufacturing experience of our CEO, Nipun Girotra. Nipun observed early in his manufacturing career that even the most sophisticated manufacturers lacked software for routine quality control and manufacturing management tasks. Where software was available, it was viewed by factory-floor employees as too difficult to use. And people either reverted to excel, or worse skipped tasks that were too burdensome. Quality problems routinely disrupted manufacturing, resulted in lost capacity, and often escaped detection with harmful impact to customers. Compliance was challenging and inefficient. So he set out to build Easy-to-Use yet Powerful Software for Quality Control and Manufacturing Management.
Oleg Nickolayev, CTO and co-founder, joined Nipun Girotra on this mission, and together, they laid the foundation for the best quality management software on the market. Oleg brought deep software development expertise and a first-principles approach to software development. The 1factory system was built ground-up with very few third-party components. This first-principles approach eliminated bloat and resulted in lightning-fast system performance.
The Problem 1factory Solves
Over the last two decades, every company has seen a dramatic increase in the number of product variants, parts and features that it needs to manage. During the same period, the pressure to reduce cost and improve capital efficiency has transformed the supporting supply chain from single-tiered and local, to multi-tiered and global.
Quality Engineers and Manufacturing Engineers now have one of the hardest jobs. On one hand, they are up against more - more features, more process complexity, more parts, more suppliers, in more locations. On the other hand, they are trying for less - shorter cycle times, lower costs, less waste, with fewer defects. In addition, they are burdened with compliance challenges. Document Control, Training Management, and Audit Readiness waste thousands of man-hours each year. Incorrect document revisions often find their way to end-users. Training is hard to track. And audit preparation consumes nearly 1/3rd of a quality manager’s time each year.
Unfortunately, their IT systems haven't kept up with increased product and supply chain complexity and compliance requirements. Quality Engineers are working on a 21st century problem with 20th century tools.
The 1factory Solution
1factory is designed to simplify the lives of Quality Control and Manufacturing engineers. 1factory simplifies every step of the quality control process and helps ensure quality within the factory and across the supply chain. The 1factory platform helps manufacturers control all aspects of product quality from drawing ballooning and quality planning through first articles, PPAPs, finished product inspection and root cause analysis. 1factory solves problems in five areas: data, analysis, access, collaboration, and compliance.
Data: Everybody has data, tons of it, that isn't the problem. The problem is it's everywhere, scattered across your factory and your supply chain, in a hundred different formats, devices, or worse yet, on paper. 1factory makes it incredibly simple to collect measurement data and link it directly to blueprints, balloons, batches, lots, gage ids, operators, and almost any other identifiers. Automated CMM imports, digital gage interfaces and barcode readers practically eliminate data entry errors. No more isolated, "islands of data". Instead, every user gets access to measurement data in the full context of its use, in real-time from within the factory and across the supply chain.
Analysis: Statistical analysis is not trivial. It's difficult to train people, and it's easy to make mistakes. Especially, when you have to analyze data for hundreds of parts and thousands of features every week. 1factory automates the statistical analysis so that you can focus on the critical task of process improvement rather than wasting your time on spreadsheets and calculations. Our powerful analytics help guide your improvement efforts.
Access: Let's face it, globally distributed, multi-tier supply chains wreak havoc on project communications. But no more. With 1factory all your partners share a single, unified view of the project, backed by a high-capacity secure "cloud" database, accessible 24 x 7 to only you and your suppliers. No more emailing spreadsheets or sharing documents. Data is instantly available to those who need it, eliminating delays, and speeding up decision making.
Collaboration: Quality problems can't be solved in isolation. You need the right people, focused on the right issue, at the right time, no matter where they are in the world. That's easy with 1factory. A built-in sharing facility provides secure access to specification and inspection data. With simple, vivid visuals, there's a common understanding of the problem and what the data
Compliance: 1factory digitizes the Quality Management System, links procedures to standards and requirements, simplifies training management, and ensures audit readiness.
The 1factory Product Development Philosophy
At 1factory, we follow a few simple rules for product management and product development. We work closely with our customers to define the problems clearly and completely. With a clear problem definition, we then design and build solutions that work for at least a sub-set of our customers. We do not customize the product. We work hard to ensure a simple and intuitive user-experience. Every interaction, field, and workflow is thoughtfully designed resulting in a delightful user experience.
Return on Investment
1factory aligns quality control expectations within groups and across companies, automates statistical calculations and reporting, speeds-up root-cause analysis, and simplifies audit preparation and compliance, allowing you to get your job done faster. Starting-up is easy, and in under two hours, you will be able to create a plan, collect data, review the analysis, and share with a customer or supplier. Unlike traditional software, where ROI may not be achieved for years, 1factory delivers an ROI within weeks. Contact us for a demo and get started today.